From Pixels to Prototypes: Struggle Bus to 200 Units
Published on July 14, 2025
Hey, isn’t this an aviation device blog? Yes, it is! But I am currently on the struggle bus trying to make the enclosures for the prototype units that I will be handing out to beta testers. I have the circuit, buttons, and knob figured out already so now the focus is on the enclosure.
The Prototyping Journey: From FDM to Injection Molding
I'm currently using a high-quality FDM 3D printer (a Bambu Lab X1), but even for early alpha units, I'm not satisfied with the finish. The layer lines and looser tolerances just don't match the professional feel I'm aiming for.
The gold standard for production-quality products is injection molding. The problem? It's designed for massive scale. The process involves a major upfront investment in molds and tooling, after which the cost per unit drops to mere cents. Most manufacturers won't even talk to you without a minimum order quantity of 5,000 units. That's a non-starter for my initial prototypes and even my projected first batch of ~200 units for Kickstarter.
Exploring the Alternatives
So, what are the options between hobbyist FDM and mass-production injection molding? The list includes technologies like SLA, SLS, and urethane casting.
My first step was to look at outsourcing. I was surprised to learn that the PaperMETAR case is considered large for many boutique manufacturers. The quotes I received were upwards of $15-20 per enclosure, even at a quantity of 200. That's simply too high to be viable.
This led me to explore bringing another technology in-house: resin printing (MSLA).
My Journey Down the Resin Printing Rabbit Hole
Having never used a resin printer, I spent the last week immersing myself in the world of MSLA. I researched printers from Elegoo, Anycubic, and Formlabs. After reaching out, Formlabs was kind enough to send some sample prints. Their quality was impressive and convinced me that resin was a path worth exploring.
While the Formlabs printers were beyond my current budget, I decided to jump in with an Elegoo Saturn 4 Ultra 12K, a wash and cure station, and some Elegoo "ABS-Like" resin. This is where my real education began (in other words, when I boarded the struggle bus!).

Resin printing promises what FDM can't: tighter tolerances and silky-smooth surfaces. The catch is that achieving those results, especially on flat, geometric parts like an enclosure, is a true art form. It requires a deep understanding of part orientation, support structures, and the entire wash/cure process.
My first print was a classic beginner's disaster—a combination of improper support, poor orientation, and over-curing.

That failure sent me back to basics: calibration. I started dialing in the printer settings for my specific resin.
After a lot of tweaking, I finally printed a complete front panel! It was a victory, but far from perfect. The surface still showed imperfections from the support structures. By now, my cleaning solution (IPA) was also getting contaminated, leaving a residue that spoiled the smooth finish I was after.
To validate my efforts, I reached out to another maker with more resin printing experience. While they also struggled to orient the part perfectly, their older, lower-resolution printer produced a much better surface finish. This was great news! It confirmed the potential is there and I just need to master the process.
A Glimmer of Hope (and a Big Reveal!)
It hasn't all been a struggle. In the midst of all this, I printed a cute, miniature version of the PaperMETAR! It's a great little reminder of the goal. I'm also excited to share the first look at the larger working prototype with you all.
The Path Forward: Urethane Casting
I haven't given up on resin printing. This experience reminds me of the steep learning curve with my first Creality FDM printer. However, my goal is a reliable process to produce up to 200 high-quality units for the Kickstarter campaign.
After more research, I believe urethane casting is the most promising next step.
The workflow looks like this:
- Create a "Master" Pattern: Use the resin printer to create one perfect, flawless version of the enclosure. This will involve meticulous post-processing like sanding and painting.
- Create a Silicone Mold: Use that master pattern to cast a flexible silicone mold.
- Cast the Final Parts: Pour the final urethane resin into the mold to produce consistent, high-quality duplicates.
My plan is to spend the next two weeks perfecting a master print and experimenting with casting. If I can't get reliable results, I will have to turn to an external manufacturer. I'm hoping to keep this in-house, as it will allow me to iterate on the design much more quickly.
Will you be at EAA AirVenture in Oshkosh?
I'm heading to AirVenture in a week! If you're going to be there, drop me a line. I'd love to meet up and chat about all things aviation.
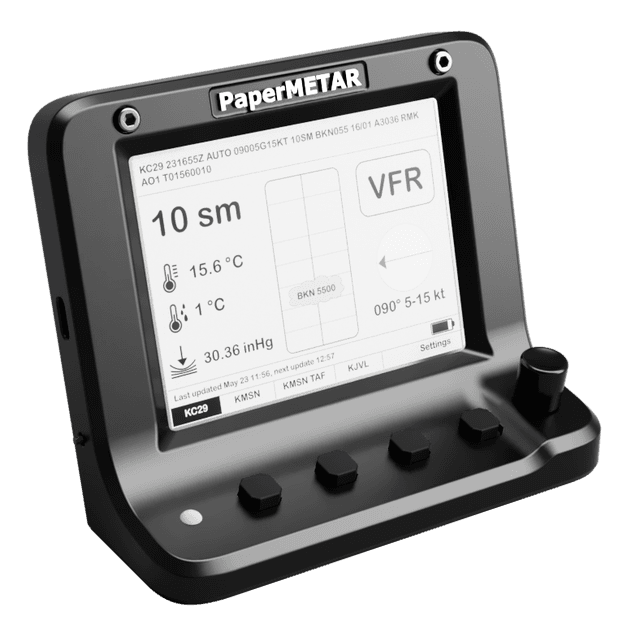
Loved this post? Let's stay connected!
- Early information on the upcoming Kickstarter campaign
- First dibs on new PaperMETAR device launches & special offers
- Firmware & API release alerts
- Pro tips for decoding METARs & TAFs